Continuous Pyrolysis Technology vs. Batch
- wastetoenergy
- May 8
- 3 min read
In the rapidly advancing field of waste-to-energy technologies, the choice between continuous and batch pyrolysis systems has significant implications for operational efficiency, scalability, and profitability. Pyrolysis, the thermal decomposition of organic materials in the absence of oxygen, offers a way to recycle a wide range of waste, including plastics, tires, and biomass. A pyrolysis plant that adopts either continuous or batch technology can have distinct advantages depending on the intended use, feedstock, and operational goals. This article examines the primary benefits of continuous pyrolysis technology over batch systems and highlights why many industries are increasingly turning to continuous processes.
Continuous Pyrolysis Technology: A Streamlined Process
Continuous pyrolysis operates on an uninterrupted feedstock input system. As materials are introduced into the continuous pyrolysis plant, the system processes them continuously, leading to constant output. This method contrasts with batch pyrolysis, where the feedstock is introduced in batches, and the reactor processes each batch before the next is added. Continuous pyrolysis provides several advantages, making it an attractive solution for large-scale operations.
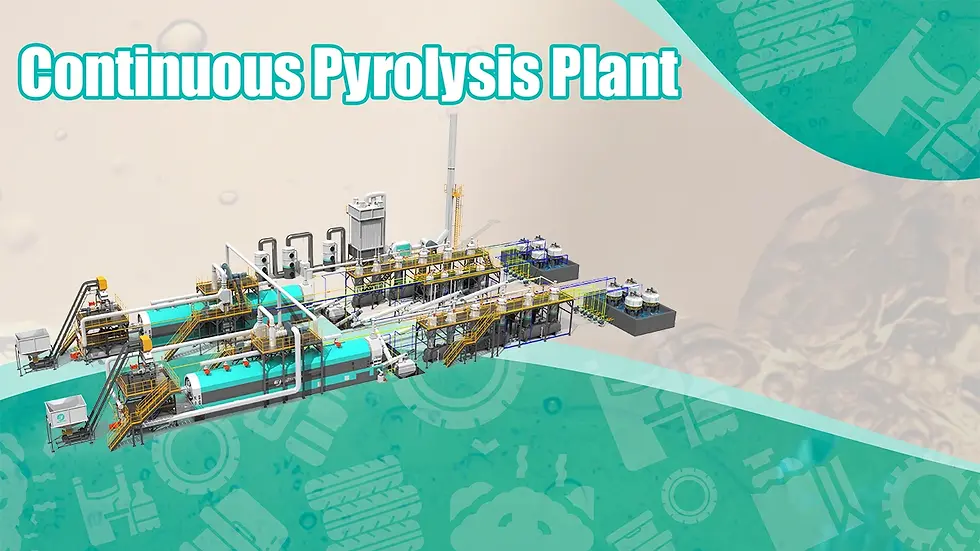
Higher Efficiency and Productivity
One of the most significant advantages of continuous pyrolysis is its ability to operate around the clock without requiring downtime for loading or unloading material. Unlike batch systems, which often have waiting times between cycles for preparation and cooling, continuous systems work in a constant flow. This operational efficiency ensures that a pyrolysis plant running continuous pyrolysis can process larger quantities of feedstock, leading to increased productivity. Moreover, with more consistent operation, the plant optimizes its energy use, reducing inefficiencies commonly associated with batch processing.
Increased Throughput and Scalability
For businesses looking to scale operations, continuous pyrolysis provides a more scalable solution than batch systems. The ability to keep feeding material into the reactor and producing output continuously allows for a greater overall throughput. As waste generation increases globally, industries require solutions that can keep pace with the demand. Continuous pyrolysis plants can accommodate larger quantities of feedstock, making them ideal for high-volume facilities and regions with large-scale waste management needs. This scalability makes continuous pyrolysis technology particularly appealing to municipalities, industrial facilities, and waste management companies.
Consistent Product Quality
The continuous nature of the process results in more consistent outputs compared to batch pyrolysis. Because the reaction conditions can be carefully controlled throughout the operation, the end products—such as bio-oil, syngas, and solid carbon—tend to have more uniform qualities. This consistency in product output is essential for industries that require specific properties in the byproducts, such as fuel or materials for industrial applications. In batch pyrolysis, variability between cycles can affect the quality of the output, leading to inefficiencies and the need for additional post-processing.
Lower Labor Costs and Automation
Continuous pyrolysis systems often require less manual intervention than batch processes. The automated systems are designed for a smooth and uninterrupted operation, reducing the need for labor-intensive tasks such as manual loading and unloading, monitoring, and cleaning. As a result, continuous pyrolysis can reduce operational costs by minimizing labor needs. Additionally, automation improves the overall safety of the plant by reducing human exposure to high-temperature environments and hazardous materials.
Batch Pyrolysis: A Comparative Look
While continuous pyrolysis offers numerous advantages, small pyrolysis machine is still a viable and cost-effective option for smaller-scale operations. In batch systems, the initial capital investment is generally lower, and the equipment is simpler, making it an accessible option for smaller businesses or experimental projects. However, the drawbacks include reduced throughput, more extended processing times, and inconsistent product quality.
Batch pyrolysis systems are best suited for operations that deal with varying types and amounts of feedstock, where flexibility is a key consideration. However, when it comes to large-scale operations, the limitations of batch processing become apparent. As feedstock requirements grow, batch systems struggle to keep up with demand due to longer downtime and more complex operational logistics.
Environmental and Economic Impact
Both continuous and batch pyrolysis systems offer environmental benefits by diverting waste from landfills and reducing the need for incineration. However, continuous pyrolysis has the added advantage of operating with better energy efficiency. The continuous processing system can recycle the heat and gases produced during pyrolysis, contributing to the energy supply of the plant. This heat recovery system further reduces the environmental footprint and improves the economic feasibility of the process.
The economic impact of continuous pyrolysis is also more favorable for high-volume operations. The ability to process larger quantities of material without downtime increases profitability over time. As the pyrolysis plant reduces waste, generates energy, and recycles valuable byproducts, it creates a sustainable revenue stream, which can be crucial for the long-term viability of the operation.
Comments