Cost Structure of a Continuous Pyrolysis Plant
- wastetoenergy
- Mar 9
- 4 min read
The cost composition of a continuous pyrolysis plant is a crucial aspect to consider when planning, operating, and scaling pyrolysis projects. Pyrolysis, the thermochemical decomposition of organic materials in the absence of oxygen, offers several benefits, including the conversion of waste into valuable products like bio-oil, syngas, and biochar. However, understanding the financial breakdown is essential for evaluating the return on investment and ensuring that the plant operates efficiently.
The financial viability of a continuous pyrolysis plant depends on numerous factors, from initial capital expenditures to ongoing operational costs. By analyzing these various components, businesses can better assess the feasibility of the investment and optimize the process to enhance profitability.
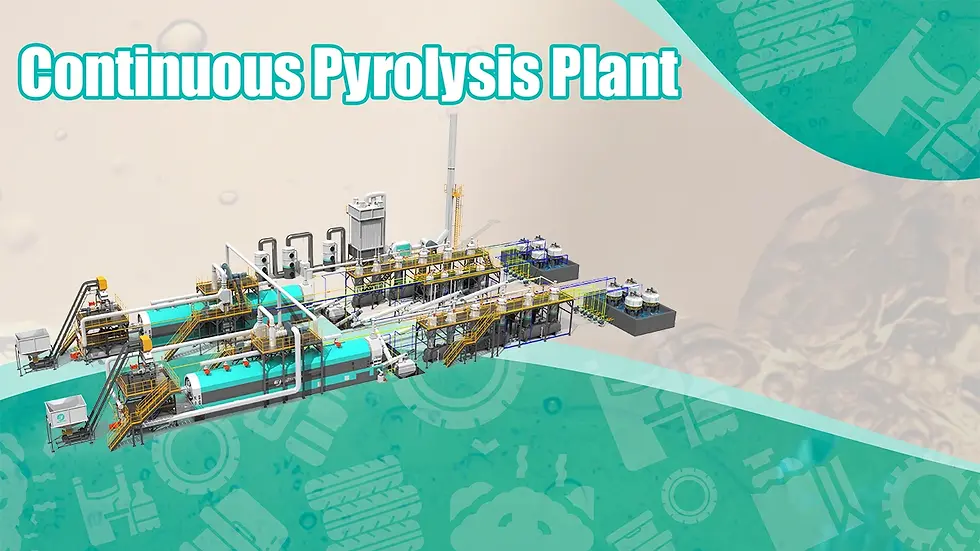
Capital Investment and Setup Costs
The initial capital investment for a continuous pyrolysis plant encompasses various components, including equipment, installation, and infrastructure development. This is often the largest cost associated with setting up the plant.
Pyrolysis Reactor: The reactor is the core component of the pyrolysis system, and its cost varies depending on its capacity, material of construction, and technological sophistication. High-quality reactors made from durable materials like stainless steel are essential for ensuring long-term performance. The size of pyrolysis reactor for sale determines its throughput capacity, and larger reactors generally come with a higher upfront cost.
Feedstock Preparation Equipment: Feedstock handling equipment includes systems for shredding, drying, and feeding materials into the reactor. For instance, when dealing with solid waste materials such as tires or plastic, machinery like shredders and conveyors are required to prepare the feedstock for pyrolysis. The complexity and automation of this equipment can add to the capital investment.
Gas Cleaning and Condensation Systems: After the pyrolysis reaction, gases such as syngas are generated. These need to be cleaned and cooled before they are either used for energy generation or sent to storage. The installation of gas cleaning and condensation systems represents another significant portion of the setup costs.
Control Systems and Automation: Automation is increasingly important in modern pyrolysis plants, where control systems manage temperature, pressure, and feeding rates. High-tech monitoring systems and automated operation help improve efficiency and minimize labor costs, but they also increase the capital investment.
Operating Costs
Once the plant is operational, ongoing expenses are incurred. These operating costs are directly related to energy consumption, labor, maintenance, and raw material procurement.
Energy Consumption: Pyrolysis is an energy-intensive process. While the plant produces some energy in the form of syngas, the rest must be sourced externally, especially during startup phases or when syngas production is insufficient. Energy costs typically make up a significant portion of operational expenses. Energy-efficient reactors and systems that recycle waste heat can help reduce these costs.
Labor Costs: Labor costs include wages for plant operators, technicians, maintenance personnel, and administrative staff. Although automation can reduce the number of manual workers needed, skilled personnel are still required to manage the plant, perform maintenance tasks, and oversee day-to-day operations. Labor costs are typically an ongoing expense that must be carefully controlled.
Feedstock Supply: The cost of acquiring feedstock, whether it is plastic waste, tires, or biomass, can fluctuate depending on the type and availability of the material. In some regions, feedstock can be sourced cheaply, while in others, it may need to be purchased at a higher cost. Efficient sourcing and establishing long-term contracts with suppliers can help stabilize this variable expense.
Maintenance and Repairs: Regular maintenance is essential to ensure the smooth operation of the pyrolysis plant. This includes replacing worn-out parts, lubricating machinery, and inspecting equipment for potential issues. Unexpected breakdowns can lead to costly repairs and unplanned downtime, so a proactive maintenance plan is critical for minimizing disruptions and ensuring continued productivity.
Environmental Compliance and Waste Management
Compliance with environmental regulations and the management of by-products also play an important role in the cost structure. Many countries have strict emissions standards for industrial operations, and failure to comply can result in fines or shutdowns. Consequently, investments in emissions control systems and waste management are necessary to meet these requirements.
Emission Control Systems: Pyrolysis plants generate gases, including volatile organic compounds (VOCs), CO2, and particulate matter. Effective emission control systems, such as scrubbers and filters, help mitigate the environmental impact of these gases and ensure compliance with air quality regulations. These systems add to the operational cost but are necessary for legal and environmental reasons.
Waste Management: In addition to gases, pyrolysis processes generate solid residues such as ash or unreacted materials. These by-products must be handled and disposed of according to local regulations. Developing a waste management strategy can mitigate disposal costs and may offer opportunities for recycling or reusing certain materials, further reducing expenses.
Revenue Generation and Return on Investment
The revenue generated by a continuous pyrolysis plant depends largely on the products it produces and the market demand for those products. Bio-oil, syngas, and biochar can be sold to various industries, creating a diversified income stream. The pricing of these products fluctuates based on market conditions, which in turn impacts the profitability of the plant.
By-Product Utilization: Efficient utilization of by-products like syngas for energy generation can offset fuel costs, reducing the plant’s dependency on external energy sources. Bio-oil can be refined into higher-value products, while biochar can be marketed as a soil amendment, offering additional revenue streams.
Product Quality: The quality of the output products also impacts their marketability. Higher-quality bio-oil, for example, can fetch higher prices in the energy market, while well-refined biochar can command a premium price in agricultural applications. Investing in technologies that improve product quality can therefore enhance revenue potential.
Carbon Credits: In some regions, pyrolysis plants may be eligible for carbon credits due to their role in waste management and reducing emissions. These credits can be sold on carbon markets, providing an additional income stream for the plant.
Comments