Enhancing Efficiency in Tyre Pyrolysis Processe
- wastetoenergy
- Jan 8
- 4 min read
Tyre pyrolysis has gained significant attention as an innovative solution for recycling waste tyres and producing valuable byproducts such as pyrolysis oil, carbon black, and steel wire. As demand for more sustainable waste management solutions increases, improving the efficiency of tyre pyrolysis systems becomes critical. By optimizing various stages of the process, operators can maximize output while minimizing energy consumption and operational costs.
Optimizing Pre-Treatment of Raw Material
The efficiency of a tire pyrolysis plant can be significantly enhanced by focusing on the pre-treatment of tyres. Tyres contain various components, including steel wire, rubber, and fabric, which can impact the pyrolysis process. Effective separation of these materials before entering the reactor ensures a more uniform feedstock, leading to higher conversion rates during pyrolysis.
Pre-cutting or shredding the tyres into smaller, more manageable pieces is a common practice to improve the heat transfer during pyrolysis. The smaller the feedstock, the faster the heating rate and the higher the yield of pyrolysis oil. Shredded tyres also allow for better control of the pyrolysis temperature, further optimizing the process.
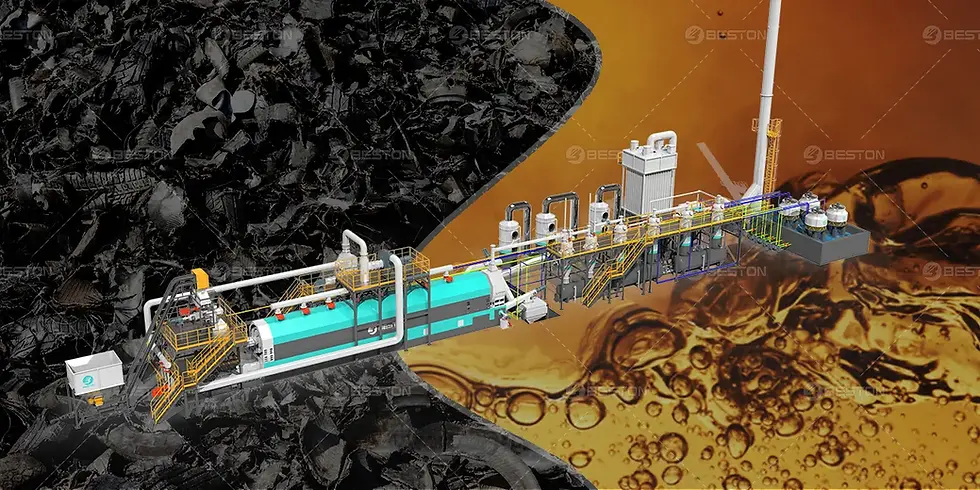
Temperature Control and Heating Optimization
The pyrolysis of tyres involves the thermal decomposition of rubber, typically at temperatures between 350°C and 500°C. The rate at which tyres are heated significantly influences the efficiency of the process. Maintaining a steady and uniform temperature throughout the reactor is crucial for maximizing pyrolysis oil yield and reducing the formation of unwanted byproducts like char and gas.
Advanced tyre pyrolysis plants, especially continuous tyre pyrolysis plant, incorporate precise temperature control systems that regulate the reactor’s heat levels more effectively. These systems use sensors and automated feedback loops to ensure that the reaction is conducted within optimal temperature ranges, thereby improving both product quality and energy efficiency.
Moreover, heat recovery systems play an essential role in reducing energy consumption. By capturing and reusing the heat generated during pyrolysis, it is possible to lower fuel requirements, thus improving the overall energy efficiency of the tyre pyrolysis plant. This can be achieved through the installation of heat exchangers and thermal storage units.
Continuous Feeding and Product Collection
A key advantage of a continuous tyre pyrolysis plant over batch systems is its ability to feed raw material into the reactor consistently while continuously extracting the products. This not only improves throughput but also enhances process stability. Continuous feeding reduces downtime and allows for a more consistent pyrolysis process, which translates into better yield and reduced energy consumption per unit of output.
The efficiency of the continuous feeding system can be further enhanced by using automated conveyor belts or screw feeders. These systems can adjust feed rates based on real-time monitoring of the reactor's conditions, ensuring a constant flow of tyres without overloading or underfeeding the reactor. Automated systems also improve safety and reduce the need for manual labor.
Effective product collection systems are equally important in maximizing efficiency. A well-designed condensate collection system ensures that the pyrolysis oil is captured without losses, while efficient gas collection systems prevent the release of volatile compounds. Both of these factors help in minimizing waste and optimizing product recovery.
Catalytic Pyrolysis for Enhanced Yield
Introducing catalysts into the pyrolysis process is another strategy to improve efficiency. Catalytic pyrolysis accelerates the breakdown of complex polymers in tyres, resulting in a higher yield of valuable hydrocarbons such as pyrolysis oil. The use of catalysts can also help reduce the formation of undesirable byproducts like char and gas, thereby enhancing the overall efficiency of the tyre pyrolysis plant.
Selecting the right catalyst is essential to optimize the process. Catalysts that promote the cracking of larger molecules into smaller, more valuable ones can increase the yield of high-quality pyrolysis oil, which can be further refined into diesel or other commercial fuels. Catalytic systems require careful monitoring to ensure that the catalyst does not degrade too quickly, which would increase operational costs.
Process Integration and Automation
Integration of advanced process control systems is another effective way to improve tyre pyrolysis efficiency. Automation technologies allow for real-time monitoring of key parameters such as temperature, pressure, and feedstock composition. By using predictive algorithms and automated control systems, it is possible to adjust operational variables dynamically to maintain optimal conditions for pyrolysis.
Process integration can also involve the coupling of tyre pyrolysis with other waste processing operations, such as gasification or bioenergy production. This can create synergies that reduce waste and improve energy efficiency. For example, excess pyrolysis gas generated during the process can be used to fuel the reactor, reducing the need for external energy sources.
Maintenance and System Optimization
Regular maintenance is crucial for ensuring that a tyre pyrolysis plant operates at peak efficiency. Over time, components such as reactors, condensers, and heat exchangers may degrade or become blocked, leading to reduced performance. Implementing a predictive maintenance schedule based on real-time monitoring data helps identify potential issues before they affect system efficiency.
Additionally, upgrading older equipment with more efficient components, such as improved thermal insulation or more advanced catalytic systems, can further boost plant performance. Continually assessing and improving system components based on technological advancements in pyrolysis can contribute to long-term efficiency gains.
Comments