Ensuring the Sealing Integrity of a Pyrolysis Reactor
- wastetoenergy
- Mar 3
- 4 min read
The sealing integrity of a pyrolysis reactor is a critical factor in ensuring efficient and safe operations. In pyrolysis, the thermal decomposition of materials occurs in a sealed, oxygen-free environment, meaning any breach in the reactor's seals can lead to safety risks, loss of valuable by-products, and decreased operational efficiency. Ensuring that the plastic reactor remains airtight and structurally sound requires a combination of proper design, material selection, routine maintenance, and monitoring.
The Importance of Sealing in Pyrolysis
A plastic reactor, or any other type of pyrolysis reactor for sale, must maintain a hermetically sealed environment to facilitate the pyrolysis process. The materials being processed, such as plastic waste, must undergo thermal decomposition at high temperatures in the absence of oxygen. If the reactor is not properly sealed, air may infiltrate the chamber, leading to incomplete decomposition, unmanageable reactions, or even hazardous combustion. Moreover, escaping gases and by-products, such as syngas or volatile organic compounds, can harm both the environment and the operational team.
To ensure proper sealing, a robust reactor design combined with suitable sealing components is essential. The reactor’s ability to contain pressure, resist corrosive substances, and withstand high operational temperatures will largely depend on the quality of its seals and gaskets.
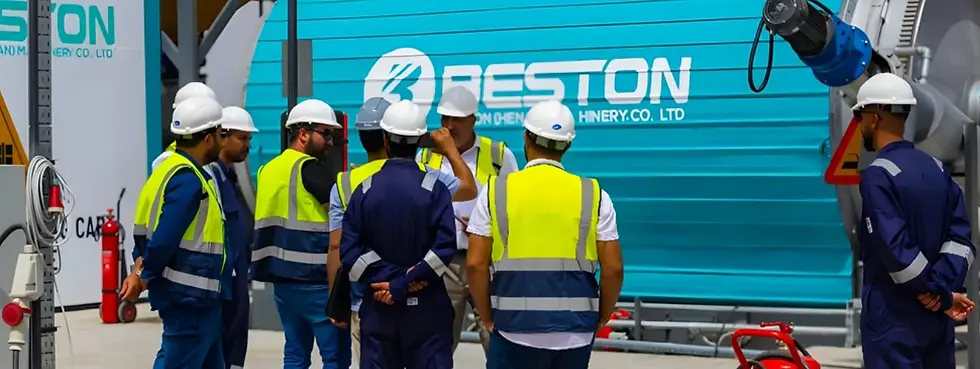
Key Elements of Sealing a Pyrolysis Reactor
1. High-Quality Gaskets and Seals
The use of high-quality gaskets and seals is fundamental to achieving a reliable seal. Gaskets must be able to handle the extreme temperatures and chemical exposure typical of the pyrolysis process. Materials such as graphite, PTFE (polytetrafluoroethylene), or ceramic-based sealing products are commonly used in pyrolysis unit due to their resistance to heat, chemicals, and wear. When selecting seals, it is crucial to assess their temperature tolerance, chemical resistance, and ability to maintain a consistent seal under varying pressure conditions.
2. Precision in Reactor Design and Fabrication
The design of the reactor itself is crucial for effective sealing. Reactor parts such as lids, hoppers, and connectors must be designed with precision to ensure tight fits. Even minor gaps in the reactor walls or joints can compromise the integrity of the system. High-quality welding techniques, such as TIG (Tungsten Inert Gas) welding, are often employed to join metal components and ensure a seamless structure. For reactors constructed from plastic or composite materials, specialized fusion or bonding techniques can provide similar levels of strength and tightness.
Additionally, the reactor must be designed to handle thermal expansion, which can lead to minor shifts in the structure during operation. These factors should be considered to prevent deformation that could affect the sealing.
3. Pressure and Temperature Regulation
The internal environment of the pyrolysis reactor often experiences high pressures and temperatures. A breach in the seal can result from temperature-induced expansion, so reactors must be equipped with pressure and temperature control systems. Monitoring and maintaining the pressure inside the reactor at an optimal level will help to avoid undue stress on the seals.
Thermal insulation around critical sealing points can also help regulate temperatures and prevent localized overheating, which may otherwise compromise seal integrity. Some reactors utilize cooling systems around sealing areas to maintain a stable temperature and prevent material degradation at the seal points.
4. Routine Maintenance and Inspections
Even the best-designed pyrolysis reactors are subject to wear and tear over time. Regular inspections and maintenance are vital to detecting early signs of seal degradation, such as cracks, leaks, or warping. Regularly checking the gaskets for signs of corrosion, loss of elasticity, or other damage can prevent catastrophic failure.
Maintenance schedules should include the replacement of seals and gaskets as needed. It is essential to keep a detailed record of the reactor's performance, as well as any repairs or upgrades to sealing components. A proactive maintenance plan can prevent costly repairs and downtime by addressing seal integrity issues before they escalate.
5. Use of Monitoring Systems
To ensure consistent sealing, modern pyrolysis reactors often incorporate monitoring systems that track pressure, temperature, and even gas leakage. These sensors can provide real-time data, helping operators detect minor deviations in the reactor's performance. Early detection of small leaks or pressure drops allows for timely intervention, ensuring the reactor's seals remain intact.
Automated systems can also alert operators when seals begin to degrade or when the internal pressure fluctuates beyond acceptable limits. This advanced technology ensures that operators can respond to potential issues immediately, preserving both the quality of the product and the safety of the system.
6. Comprehensive Testing and Validation
Before starting operations, it is essential to conduct rigorous testing to validate the sealing of the pyrolysis reactor. Leak testing, vacuum tests, and pressure tests are common practices used to ensure that the reactor can maintain an airtight environment under operational conditions. These tests should be repeated at regular intervals throughout the lifespan of the reactor.
Furthermore, running test batches at varied temperatures and pressures will help ensure that the reactor can consistently perform under different operating scenarios, confirming that the seals hold up under stress.
Comments