Strategies to Reduce Operating Expenses in Pyrolysis Plant Management
- wastetoenergy
- May 12
- 3 min read
Managing a pyrolysis plant involves significant operational expenditures that directly impact profitability. Optimizing these costs without compromising output quality or safety requires a meticulous approach, combining technological innovation with process refinement. Understanding the key contributors to pyrolysis plant cost is essential for implementing effective cost-control strategies.
Energy Efficiency and Consumption Control
Energy consumption constitutes a substantial fraction of operating expenses in a pyrolysis plant. Thermal processes demand sustained high temperatures, often ranging between 350°C and 550°C, to achieve effective feedstock conversion. Inefficient heat management leads to excessive fuel usage, inflating operational costs.
Optimizing thermal insulation and incorporating advanced heat recovery systems can drastically reduce energy input requirements. For instance, waste heat exchangers reclaim residual thermal energy from flue gases, preheating incoming feedstock or combustion air. This reuse of heat reduces dependency on external fuel sources and lowers overall energy expenditure.
Additionally, integrating automated temperature control systems stabilizes reactor conditions, preventing energy waste caused by overheating or thermal fluctuations. Continuous monitoring and predictive maintenance further minimize energy loss by ensuring that heating elements and burners operate at peak efficiency.
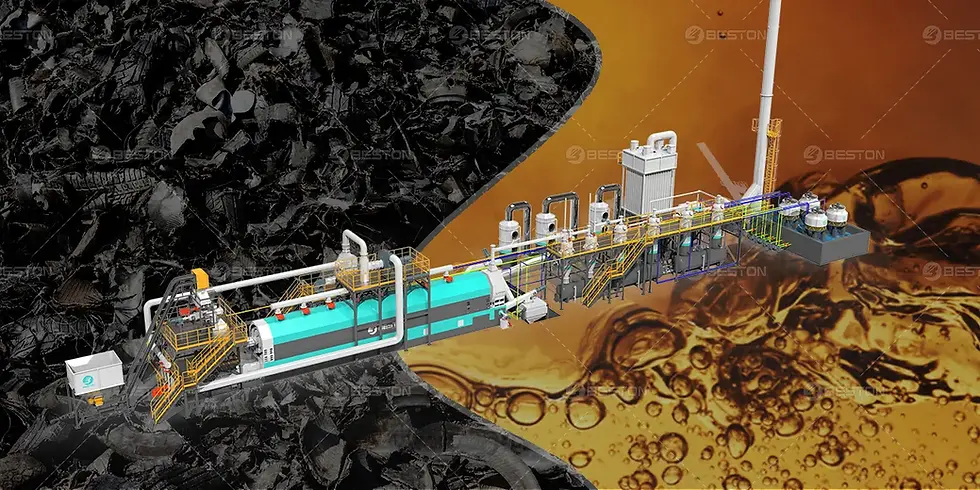
Feedstock Management and Preparation
Feedstock variability can elevate the pyrolysis plant cost through inefficient processing and increased maintenance demands. Feedstocks with high moisture or impurity content reduce thermal efficiency and promote fouling or corrosion in reactor components.
Investing in preprocessing units such as shredders, dryers, or contaminant separators enhances feedstock homogeneity. Properly prepared feedstock ensures stable pyrolysis reactions and improves the yield of valuable byproducts like pyrolysis oil and char. Although preprocessing adds upfront costs, it ultimately decreases downtime and repair expenses by mitigating equipment wear.
Furthermore, sourcing feedstock locally or establishing long-term supply agreements reduces transportation expenses and price volatility. A reliable feedstock supply chain is fundamental to controlling operational expenditure.
Process Automation and Control Systems
Modern pyrolysis plants benefit significantly from advanced automation technologies. Real-time sensors monitor parameters such as temperature, pressure, gas composition, and feedstock throughput. These data streams enable centralized control systems to adjust operational variables dynamically, optimizing the pyrolysis reaction and minimizing resource consumption.
Automation also reduces labor costs by limiting the need for manual intervention and enabling predictive maintenance schedules. Early detection of mechanical issues prevents catastrophic failures that cause costly shutdowns and repairs.
Deploying programmable logic controllers (PLCs) and integrating them with supervisory control and data acquisition (SCADA) systems enhances process transparency and operational responsiveness, which are crucial for minimizing inefficiencies and unexpected expenses.
Byproduct Utilization and Revenue Maximization
Efficient management of pyrolysis byproducts directly influences the economic viability and operational cost structure of the plant. Pyrolysis oil, gas, and char possess considerable commercial value when processed or sold effectively.
Recycling combustible gases generated during pyrolysis as a supplementary energy source lowers external fuel demand, thereby reducing pyrolysis plant cost. Optimizing gas capture and combustion systems maximizes this internal energy recycling.
Additionally, upgrading pyrolysis oil through refining or blending can increase its market value. Char, often used as biochar or activated carbon, opens avenues for additional revenue streams. Establishing downstream partnerships for byproduct utilization transforms waste into profit and offsets operational expenses.
Maintenance Optimization and Equipment Longevity
Unexpected equipment failure imposes substantial repair costs and production interruptions. Implementing rigorous preventive maintenance protocols extends the lifespan of critical components like reactors, condensers, and feeding systems.
Condition-based maintenance, facilitated by continuous monitoring of vibration, temperature, and pressure, enables targeted interventions before failure occurs. Employing corrosion-resistant materials and modular reactor designs simplifies repairs and reduces downtime.
Investing in quality components initially may increase capital outlay but results in lower pyrolysis plant cost over time by decreasing the frequency of replacements and emergency repairs.
Regulatory Compliance and Environmental Management
Non-compliance with environmental and safety regulations can incur heavy fines, legal fees, and forced shutdowns. Allocating resources to maintain emissions control technologies—such as scrubbers, filters, and catalytic converters—prevents costly regulatory breaches.
Effective waste management protocols reduce disposal fees and potential liabilities. Moreover, adopting environmentally sound practices enhances corporate reputation, potentially opening access to incentives or subsidies that mitigate operating costs.
Comments