Tire Pyrolysis: Converting Waste Rubber into Usable Energy Streams
- wastetoenergy
- May 14
- 3 min read
End-of-life tires represent a persistent environmental challenge due to their durability and resistance to degradation. As global production of vehicle tires continues to rise, sustainable disposal and valorization strategies become critical. Among these, thermal decomposition via a pyrolysis plant has emerged as a commercially viable and environmentally aligned method for transforming discarded rubber into valuable secondary products.
Harnessing Thermal Decomposition for Material Recovery
Tire pyrolysis plant employs an oxygen-free thermal process to decompose complex hydrocarbons in vulcanized rubber. Operating typically between 400°C and 600°C, the pyrolysis reactor breaks down tire polymers into smaller molecular compounds. The result is a trio of end products: pyrolytic oil, combustible gas, and solid carbon residue.
This transformation pathway reduces volumetric waste while unlocking embedded energy content. Each metric ton of scrap tire processed yields approximately 450 kg of oil, 150 kg of carbon black, 100 kg of steel, and 100 kg of syngas—offering both material and calorific recovery.
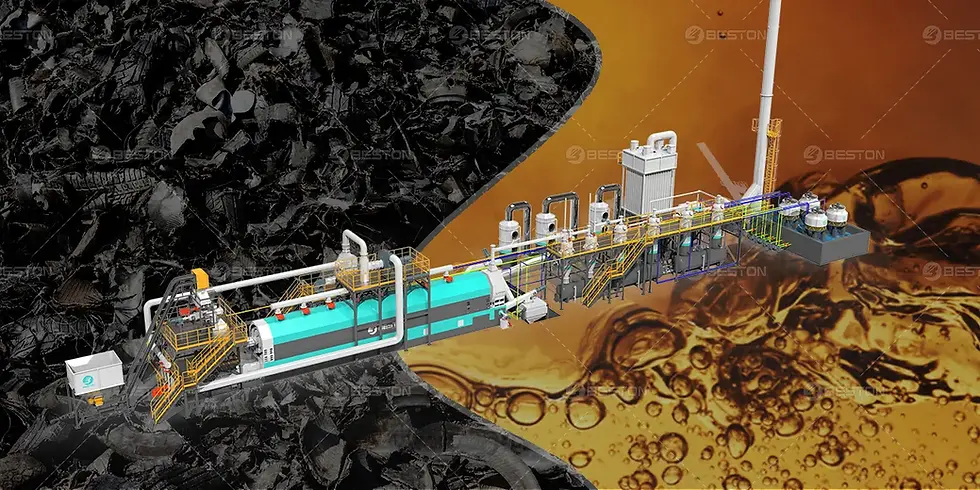
Pyrolysis Oil as a Renewable Liquid Fuel
Pyrolysis oil, often referred to as TPO (tire pyrolysis oil), has heating values comparable to conventional diesel. After post-processing to remove sulfur and ash content, it becomes suitable for industrial furnaces, power generation, and, in certain cases, maritime fuel applications.
Its chemical composition, rich in aromatic hydrocarbons, lends itself to further upgrading through hydrogenation or cracking. When integrated into circular fuel systems, TPO displaces fossil-derived alternatives, contributing to decarbonization goals in heavy industry and energy-intensive sectors.
Steel Wire Recovery and Secondary Use
Tires contain approximately 10–15% steel by weight. During pyrolysis, embedded steel wire is liberated from the rubber matrix and can be magnetically separated. Recovered steel maintains structural integrity and can be recycled into smelting or casting operations, thereby reintegrating into industrial supply chains without loss of material quality.
This diversion of high-tensile steel from landfills eliminates the environmental burden of buried metallic waste and reduces the demand for virgin ore extraction.
Carbon Black Revalorization
The solid residue from tire pyrolysis, known as recovered carbon black (rCB), holds commercial value when treated appropriately. While not identical to virgin carbon black used in tire manufacturing, rCB can be upgraded through grinding, activation, or pelletization to serve in pigment production, rubber compounding, or as a filler in plastic and construction materials.
A properly configured waste tyre pyrolysis plant ensures minimal ash content in the rCB output, increasing its compatibility with downstream applications and boosting overall plant profitability.
Process Gas for Internal Energy Circulation
A critical component of tire pyrolysis energy efficiency is the utilization of non-condensable gas. Rich in methane, hydrogen, and light hydrocarbons, this synthetic gas is routed back to heat the reactor or auxiliary burners. This intrinsic energy loop reduces the need for external fuels, stabilizes operating temperatures, and minimizes greenhouse gas emissions.
Advanced systems integrate gas cleaning and compression modules, allowing for consistent pressure and cleaner combustion—key factors in maintaining emission compliance.
Continuous Operation Enhances Sustainability
For high-throughput facilities, continuous pyrolysis reactors offer superior thermal consistency and material handling. These systems automate feedstock input and product extraction, reducing downtime and energy wastage associated with batch-mode operations.
By maintaining a constant thermal profile, continuous systems optimize heat exchange efficiency, enhance oil yield, and support real-time process adjustments. Such configurations are indispensable for large-scale tire recycling operations aiming for minimal environmental impact and maximum resource recovery.
Regulatory Compliance and Lifecycle Benefits
Tire pyrolysis aligns with extended producer responsibility (EPR) policies and circular economy principles. Properly licensed plants comply with emissions thresholds for volatile organic compounds (VOCs), sulfur oxides, and particulate matter, ensuring environmental acceptability.
Moreover, life cycle assessments indicate a net reduction in CO₂ equivalent emissions when tire pyrolysis substitutes incineration or landfill. Material recirculation and energy substitution reinforce its role as a sustainable waste-to-energy mechanism in modern industrial ecosystems.
Comments