Working Principle of Thermal Desorption Unit
- wastetoenergy
- Jul 21, 2024
- 4 min read
In the quest for effective remediation technologies, the thermal desorption unit (TDU) has emerged as a pivotal innovation in managing hazardous waste, particularly oil sludge. This article explores the working principle of the TDU, highlighting its components, process dynamics, and applications in waste management and environmental remediation.
Overview of Thermal Desorption Technology
Thermal desorption technology is a non-combustive method that employs heat to volatilize contaminants from solid matrices. Unlike incineration, which destroys waste through combustion, thermal desorption focuses on separating hazardous constituents from the bulk material. This separation enables the recovery and potential reuse of both the cleaned solid and the extracted contaminants.
Key Components of a Thermal Desorption Unit
A thermal desorption unit comprises several critical components that facilitate the efficient separation of contaminants:
Feed System: This component introduces the contaminated material into the TDU. It typically includes conveyors or screw feeders designed to handle various types of input materials, such as oil sludge, contaminated soil, or industrial waste.
Desorption Chamber: The heart of the TDU, where heat is applied to volatilize the contaminants. The chamber is often a rotary kiln or a static oven, equipped with mechanisms to ensure uniform heating and thorough mixing of the material.
Heating System: This system provides the necessary thermal energy to the desorption chamber. It may include burners or electric heaters capable of maintaining precise temperature control. The heat source is selected based on the nature of the contaminants and the desired desorption temperature.
Off-Gas Treatment System: As contaminants are volatilized, they form an off-gas stream that requires treatment. This system typically includes condensers, scrubbers, and filters to capture and treat volatile organic compounds (VOCs) and other gaseous emissions.
Residue Management System: After desorption, the treated solid material is discharged from the unit. This system may include cooling mechanisms and conveyors to handle the residue efficiently.
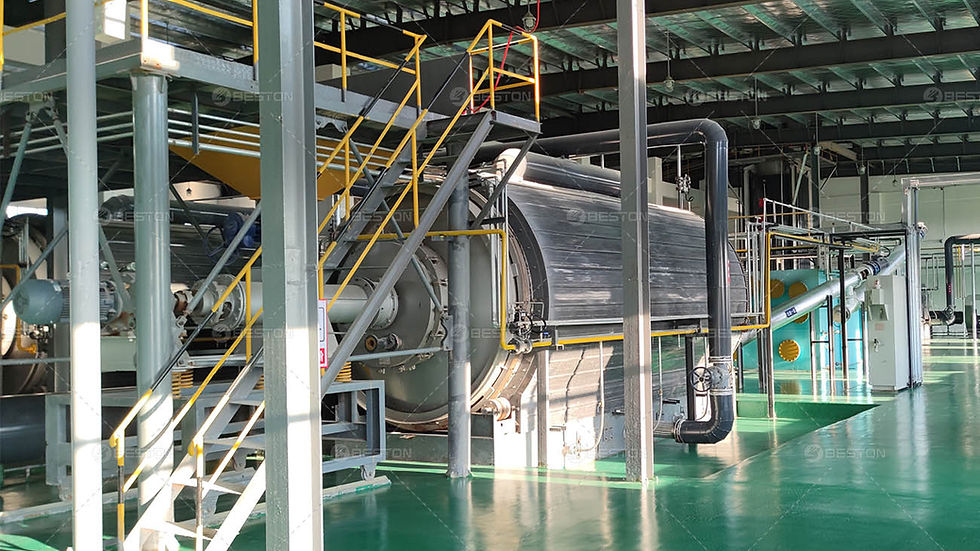
Process Dynamics of Thermal Desorption
The thermal desorption process involves several key stages, each contributing to the effective removal of contaminants:
Pre-treatment: Before entering the desorption chamber, the contaminated material undergoes pre-treatment to ensure uniform particle size and moisture content. This step enhances the efficiency of heat transfer and volatilization.
Heating and Desorption: In the desorption chamber, the material is exposed to controlled heat. The temperature is carefully regulated to volatilize specific contaminants without causing thermal degradation of the bulk material. The choice of temperature depends on the boiling points of the target contaminants.
Off-Gas Collection: As contaminants are volatilized, they form an off-gas stream that is collected and directed to the off-gas treatment system. This stage is critical for preventing the release of harmful emissions into the environment.
Condensation and Recovery: Within the off-gas treatment system, condensers cool the gas stream, allowing the separation of volatile compounds. These compounds can be recovered as liquid or gaseous fractions, which may be reused or further processed.
Residue Discharge: After desorption, the treated solid residue is discharged from the chamber. This material, now free of hazardous contaminants, can be safely disposed of or repurposed, depending on its composition.
Advantages of Thermal Desorption Units
Thermal desorption units offer several advantages over traditional waste management methods:
Selective Contaminant Removal: Unlike incineration, which indiscriminately destroys all material, thermal desorption selectively removes contaminants, allowing for the potential reuse of the cleaned material.
Versatility: TDUs can handle a wide range of contaminated materials, from soil and sediments to industrial sludges and drill cuttings. This versatility makes them suitable for various remediation scenarios.
Reduced Waste Volume: By volatilizing only the contaminants, TDUs significantly reduce the volume of waste that requires disposal. This reduction lowers disposal costs and minimizes the environmental footprint of waste management operations.
Resource Recovery: The process enables the recovery of valuable hydrocarbons and other compounds from the off-gas stream. These recovered materials can be used as alternative fuels or raw materials in industrial processes.
Environmental Compliance: TDUs are designed to meet stringent environmental regulations, ensuring that emissions are controlled and minimized. The off-gas treatment system plays a crucial role in achieving compliance with air quality standards.
Applications of Thermal Desorption Units
Thermal desorption units find applications in various industries and environmental remediation projects:
Oil and Gas Industry: TDUs are extensively used in the oil and gas sector to treat drill cuttings, tank bottoms, and other oil-contaminated wastes. The ability to recover hydrocarbons from these wastes adds economic value to the remediation process.
Hazardous Waste Management: Industries generating hazardous waste, such as chemical manufacturing and pharmaceuticals, employ TDUs to detoxify contaminated solids and reduce the volume of waste requiring disposal.
Environmental Remediation: In contaminated site cleanup projects, pyrolysis unit is used to treat soil and sediments containing volatile organic compounds, pesticides, and other pollutants. The technology is particularly effective for sites with a history of industrial activity.
Municipal Waste Treatment: Thermal desorption technology is increasingly being applied to municipal waste treatment, particularly for the management of sewage sludge and other organic wastes. The process aids in reducing the volume and toxicity of waste materials.
Challenges and Considerations
While thermal desorption units offer significant advantages, several challenges and considerations must be addressed:
Energy Consumption: The heating process requires substantial energy input, which can impact the overall cost and environmental footprint of the operation. Optimizing energy efficiency is crucial for sustainable implementation.
Material Handling: The design of the feed and residue management systems must accommodate diverse waste types and ensure consistent material flow. Proper handling minimizes the risk of blockages and equipment wear.
Temperature Control: Precise temperature control is essential to achieve effective desorption without causing thermal degradation of the material. Advanced control systems and real-time monitoring are often employed to maintain optimal conditions.
Off-Gas Treatment: The composition of the off-gas stream can vary depending on the nature of the contaminants. Designing an effective treatment system requires careful consideration of the expected emissions and regulatory requirements.
Residue Disposal: The treated residue may still contain trace contaminants or altered chemical properties. Proper testing and analysis are necessary to determine suitable disposal or reuse options.
Future Developments in Thermal Desorption Technology
As environmental regulations become more stringent and industries seek sustainable waste management solutions, thermal desorption technology continues to evolve. Future developments may focus on enhancing energy efficiency, improving off-gas treatment systems, and expanding the range of treatable contaminants. Advances in automation and real-time monitoring will further optimize the performance and reliability of thermal desorption units.
In conclusion, the thermal desorption unit represents a significant advancement in waste management and environmental remediation. Its ability to selectively remove contaminants while enabling resource recovery makes it a valuable tool in the pursuit of sustainable and effective waste treatment solutions.
Comments